研究内容
当研究室では、現在、求める特性を発現する材料の設計と、それを実際に製造するためのプロセスの開発に関する研究を、先端的な実験研究と計算機シミュレーションや機械学習などの計算研究を融合させて展開しています。 具体的には、金属3Dプリントプロセスや、金属3Dプリントプロセスで用いられるレーザーや電子ビームによる溶融・凝固を活用した新材料の創製に取り組んでいます。
この分野の研究は、世界中で盛んに行われるようになってきていますが、その中で私たちの研究の特徴として、金属3Dプリントにおいて発現することが見出された結晶配向を、プロセスモニタリングやコンピュータシミュレーションと組み合わせることで、従来の凝固・結晶成長の研究ではあまり扱われてこなかった凝固条件下での結晶成長の特徴を明らかにし、その特徴を活かして、これまで不可能であった特性の発現を可能にする研究を行っています。(例えば、 Okugawa, M. et al. Solute segregation in a rapidly solidified Hastelloy-X Ni-based superalloy during laser powder bed fusion investigated by phase-field simulations and computational thermal-fluid dynamics. Addit. Manuf. 84, 104079 (2024).)
さらに、これまでは単結晶化してから最適な熱処理プロセスを施すことで有用な特性を発現することが分かっていながら、高コストや形状付与の困難さから実用化に至らなかった物質(例えば、鉄とアルミニウムの化合物であるFe3 Al)を、単結晶化しながら部品形状を付与する新しいプロセスを開発することで、これまで「物質」に留まっていた材料候補を実用に適う「材料」とする研究も進めています。加えて、新しいプロセスを通じて、特有の材料特性を発現させることにも取り組んでいます。
小泉は、科学研究費 学術変革領域研究(A)「超温度場材料:巨大ポテンシャル勾配による原子配列制御が拓くネオ3Dプリント」 の領域代表を務めています。研究室のメンバーの多くがこの領域の研究に携わっています。この研究領域では、レーザーや電子ビームと物質との相互作用で形成される極限的な温度勾配(107 K/m以上を超温度場と定義)下での急速冷却、急速凝固・結晶成長に注目した新材料の創製に関する研究を、大阪大学大学院工学研究科 異方性カスタム設計AM研究開発センター(センター長:中野貴由教授)の支援を受け、全国の共同研究者とともに展開しています。本領域において当研究室の、小泉、奥川、柳は、計画研究A01a 超温度場デジタルツイン科学を担当し、3Dプリントにおける単結晶化のプロセスのモニタリング(例えば、Liu, Y., Nose, K., Okugawa, M., Koizumi, Y. & Nakano, T. Fabrication and Process Monitoring of 316L Stainless Steel by Laser Powder Bed Fusion with µ-Helix Scanning Strategy and Narrow Scanning Line Intervals. Mater. Trans. 64, 1135–1142 (2023).)、溶融・凝固挙動のコンピュータシミュレーション、さらには、3Dプリント後の熱処理最適化による材料特性向上のための組織制御の実験・計算融合研究(例えば、Liu, Y. et al. Resolving the long-standing discrepancy in Fe3Al ordering mobilities: A synergistic experimental and phase-field study. Acta Mater. 273, 119958 (2024).)にも取り組んでいます。(プレスリリースなど)
さらに、Additive Manufacturing(3Dプリント)で実現できる形状の自由度を利用し、元来その物質が発現し得ない特性を形状の付与によって実現する「メタマテリアル」の研究にも取り組んでいます。その中でも、負の屈折率で注目されているメタマテリアルの中から、荷重に対する応答が特殊な力学メタマテリアル(Mechanical Metamaterial)の研究を進めています。この研究では、結晶性材料の変形や力学特性の研究で培ってきた知見を元に、形状の付与によって相転移を発現させることで塑性変形を発現させることに取り組んでいます。形状付与後に形状がさらに変化する3Dプリントは「4Dプリント」と呼ばれ、新しい研究分野として注目されています。(例えば、 Kanegae, S., Okugawa, M. & Koizumi, Y. Martensitic Phase-Transforming Metamaterial: Concept and Model. Materials 16, 6854 (2023))
小泉は、阪神淡路大震災や東日本大震災を経験したということもあり、防災や減災に役立つメタマテリアルの開発に強いモチベーションを持っています。また、スポーツにおける事故や予期できない事件により命が奪われたり身体能力を喪失したりすることを防ぐためのメタマテリアルの開発にも取り組んでいます。加えて、エネルギー問題や地球温暖化に起因すると考えられる災害を抑えるため、カーボンニュートラルや資源循環に貢献するリサイクル技術の開発にも、独自の視点で研究を進めています。
The high strength of Al-Si hypoeutectic alloys additively manufactured by powder-bed fusion is of great scientific interest. To date, the mechanism of grain refinement near the fusion line, which contradicts conventional Hunt’s columnar–equiaxed transition criteria, remains to be elucidated. Here we present the first report on the mechanism of grain refinement. When a laser was irradiated on cast Al-Si alloy consisting of coarse α-Al grain and α-Al/Si eutectic regions, grain refinement occurred only near the eutectic regions. This strongly suggests that the Si phase is crucial for grain refinement. Multi-phase-field simulation re- vealed that rapid heating due to the laser irradiation results in unmelted Si particles even above the liquidus temperature and that the particles act as heterogeneous nucleation sites during the subsequent re-solidi- fication. These results suggest the feasibility of a novel inoculant-free grain refinement that is applicable to eutectic alloys comprising phases with a significant melting point difference. “Equiaxed grain formation by intrinsic heterogeneous nucleation via rapid heating and cooling in additive manufacturing of aluminum-silicon hypoeutectic alloy” Masayuki Okugawa, Yuta Ohigashi, Yuya Furishiro, Yuichiro Koizumi, Takayoshi Nakano Journal of Alloy and Compounds, Vol. 919 (2022) 165812. https://doi.org/10.1016/j.jallcom.2022.165812
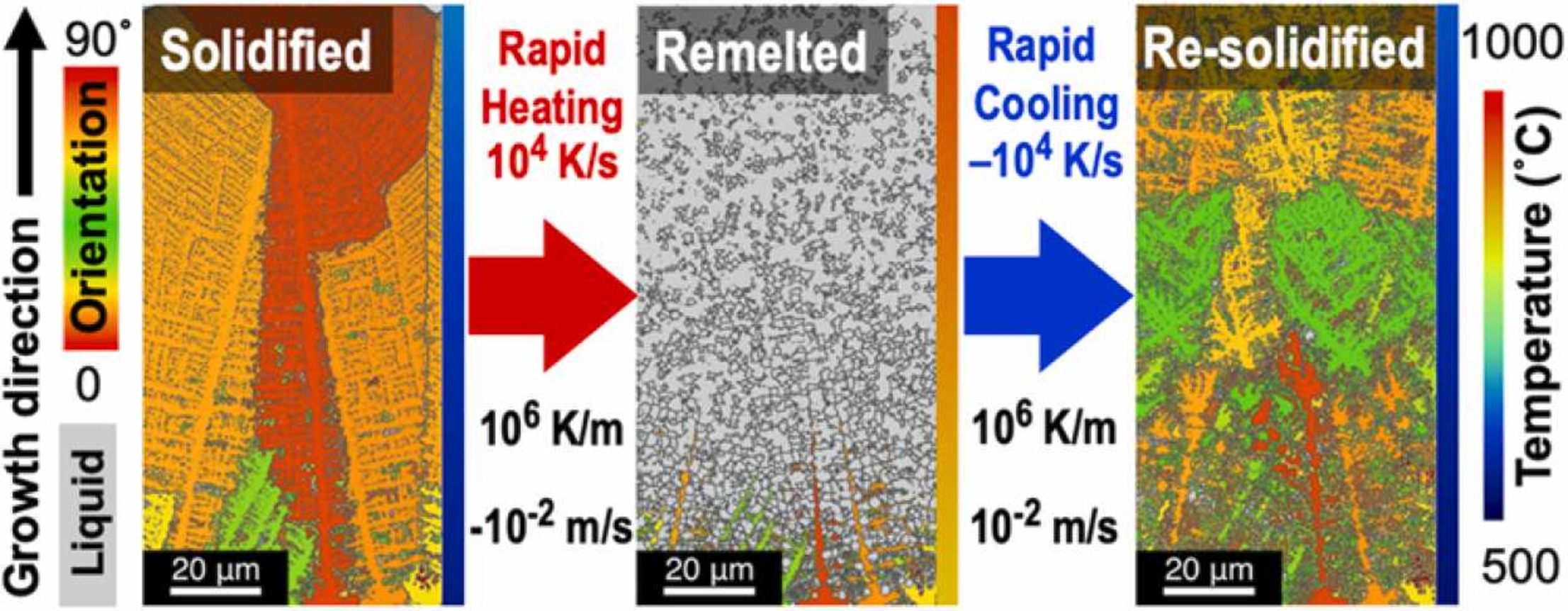
本研究では、直接計測が困難な現象を観測データと整合させた計算機シミュレーショ ンの解析で推定するデジタルツイン科学手法を開発し、それを駆使して粉末床溶融結 合(PBF)型付加製造(Additive Manufacturing)と呼ばれる金属3Dプリント (3DP)で発現する特有の結晶成長を理解しすることを目指しています。さらに、固 液界面での温度勾配や界面移動速度などの凝固条件と材料組織との関係を、従来対象 とされてきた範囲を超えた条件で解明し、新しい結晶成長の世界を開拓しています。 これにより、金属3DPを材料に形状を与えるだけでなく、適材適所に単結晶から微細 粒まで結晶組織の制御により最適な材料特性を与える方法として発展させるための学 理を構築を進めています。
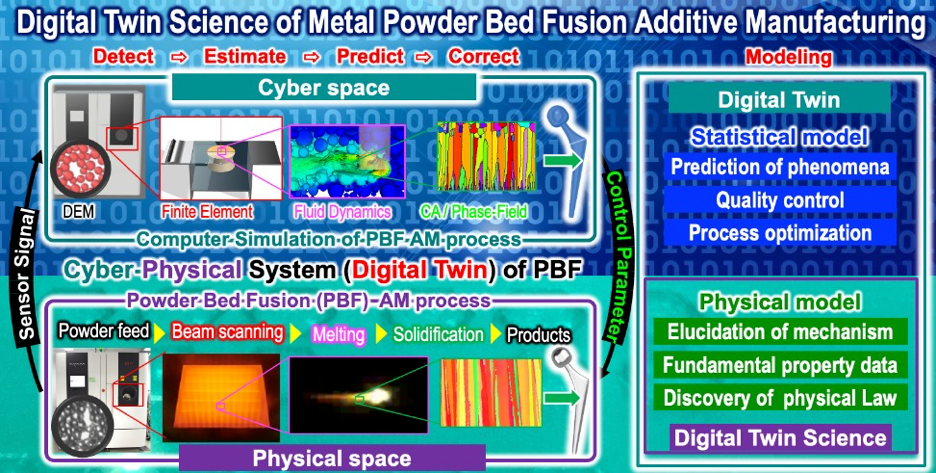
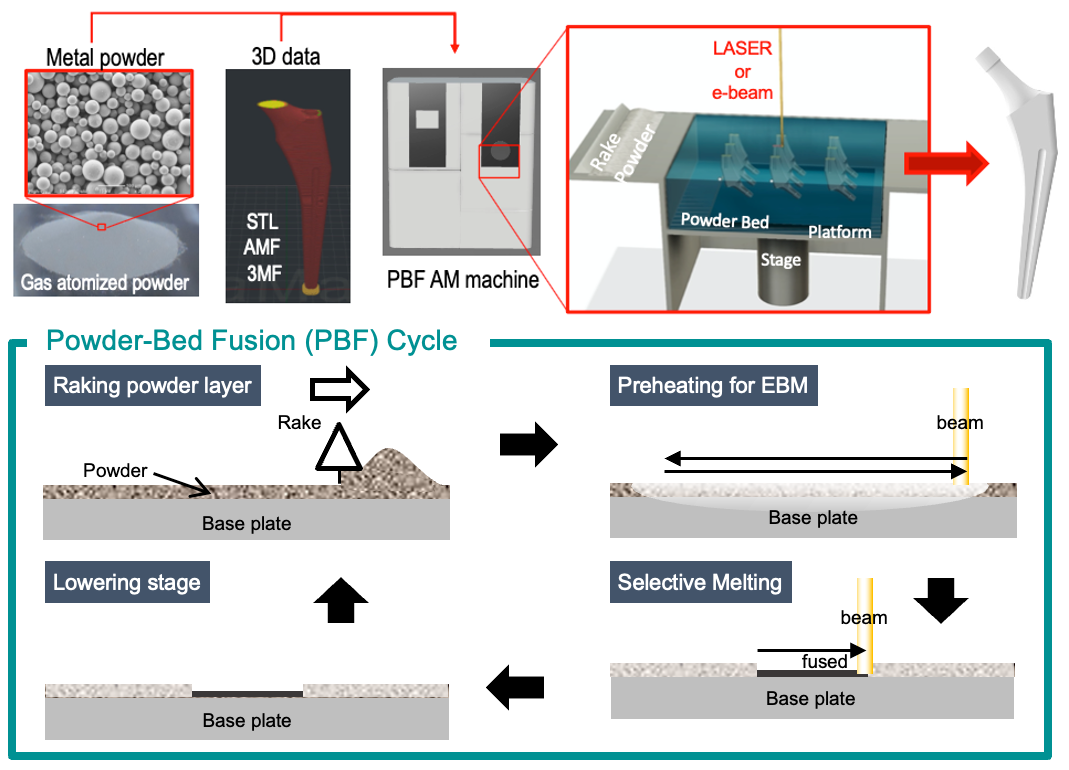
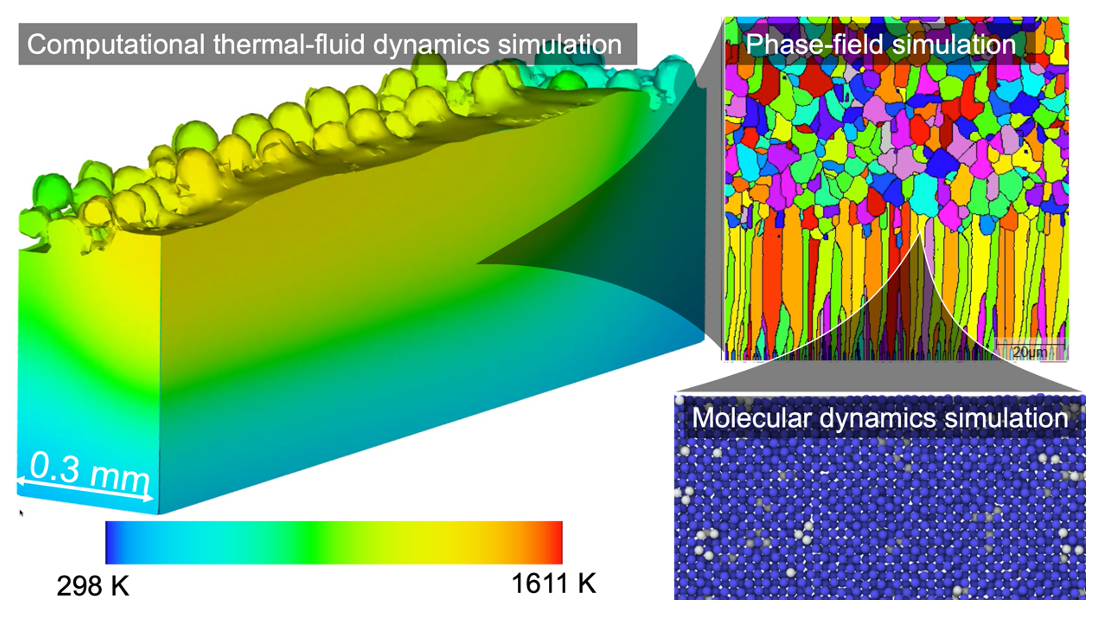
3Dプリント技術は,鋳型等を必要とせず形状データから直接部材を製造できることから,製造業に革新を産む技術として強く期待されています。すでに一部の材料では無欠陥(無気孔,無亀裂)の造形物を得るための造形条件最適化が試行錯誤的になされ,実用レベルに達しているものの,実用材料の全てが3Dプリントできているわけではありません.特に金属部材の製造では,従来,加工・熱処理プロセスを経て必要な材料特性が得られて来ました。そのため気孔等の欠陥のない造形物がができたとしても,必要な材料特性が得られるとは限りません.そのため,材料の各種物性と最適条件との間の法則を見出し,試行錯誤によらない金属材料の造形条件最適化を可能とし、材料特性を決定する材料組織を造形プロセス中に制御するための指導原理を確立することが求められています。私達は、そのような3Dプリント技術の確立を目指して、実験と計算を相補的に融合した研究に取り組んでいます。
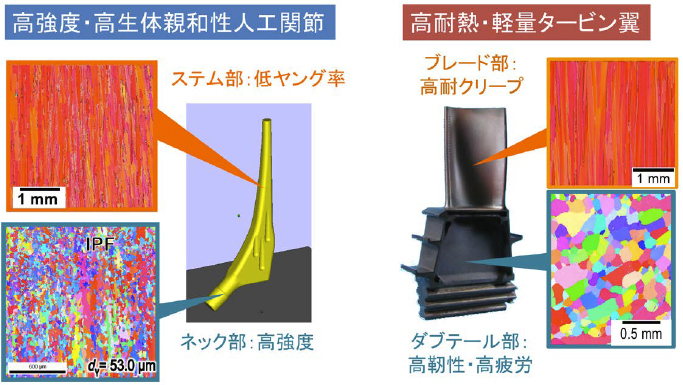
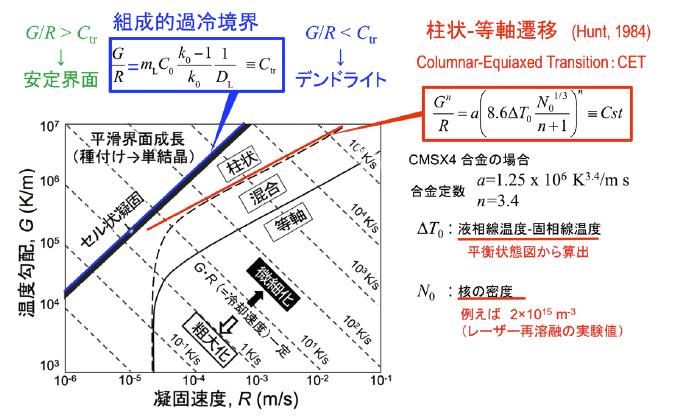
金属3Dプリントにおける自在な材料組織制御のため、柱状—等軸遷移等、鋳造や溶接の研究で培われてきた知見を基軸としながらも、それらとの違いとして、「1mm以下の溶融領域サイズ」、「粉末粒子の溶融に伴う複雑な融液流動」、「最大8千m/sの高速熱源移動」に由来した特殊環境における特有の溶融凝固現象が組織形成に及ぼす影響を解明し、部位毎に組織を最適化した部材の製造や、従来プロセスでは不可能な組織制御による高性能材料創製に資する、新しい研究分野の礎を築くことを目指しています。
このテーマは、小泉が約10年前の2007年にMITのSamuel Allen 教授との共同研究で開始した研究で、計算機シミュレーションを用いた研究を始めるきっかけとなった研究テーマです。当初は、規則合金中の原子の規則配列の乱れによって生じる逆位相領域境界(AntiPhase Domain Boundary: APDB)と原子空孔との相互作用の影響に注目した研究から始めました。現在では、より後半な材料で形成される広義の積層欠陥(すべり変形で導入される積層欠陥、双晶境界、半整合異相界面等)と溶質元素との相互作用が組織形成の速度論(カイネティックス)や組織の安定性に与える影響を界面する研究を行っています。研究開始当初はあまり注目されませんでしたが、最近この研究の成果が参照されるようになってきています。こうした研究は、加工性に優れかつ高温強度に優れる耐熱バネ用材料や、次世代のガスタービン翼材料の開発や信頼性の向上に役立つとものと期待されています。
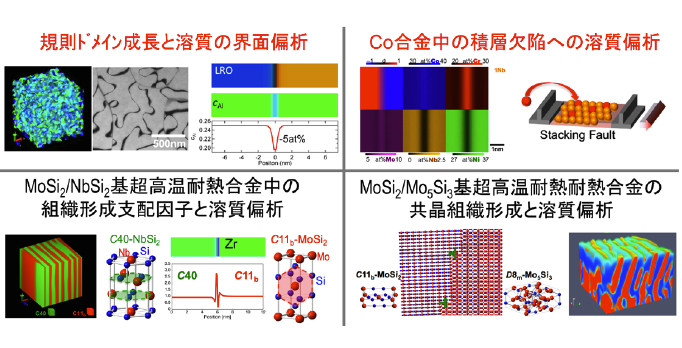
一般に3Dプリントとして知られる技術は、材料を継ぎ足して形状を作るため付加製造(Additive Manufacturing)と呼ばれ、切削、鋳造、塑性加工といった従来の加工方法では製造が不可能あるいは極めて困難な形状を容易に作り出すことができます。特に、数十µm〜数百mm程度の解像度で数mm〜数百mm程度の大きさの部材が製造できる技術がこの2010年頃以降から急速に発達しました。このことは非常に大きな意味を持っています。
三次元的に材料を積み上げて構造を作る技術は半導体素子や回路の製造のために1980年代から急速に発達し今日の情報・通信社会を実現してきました。現在もそのような技術の研究は発展し続けています。特にnmオーダーの構造を有する材料が、量子効果によりバルク材とは異なる物性を示すため、その現象自体が科学研究の対象となり、様々な新しい現象が見出され、それらを利用した素子が開発されてきました。
一方、最近の3Dプリント技術は数十µm程度以上、つまり私達が肉眼で見たり、手で触れるサイズの材料が発現するのと同様の特性を示す材料を自在に3次元的に配置することが可能です。したがって、従来の古典的な材料の特性を知識により造形する部材の特性を設計することが可能です。このことにより、予め求める特性を実現するための微細構造を設計し、それを造形することで求める特性を発現する多孔質材料や格子構造をもつ材料を得ることができます。これにより、例えば強度を維持しつつ剛性を下げることで、骨との力学的親和性に優れかつ強度信頼性の高い人工関節用材料の製造が可能です。
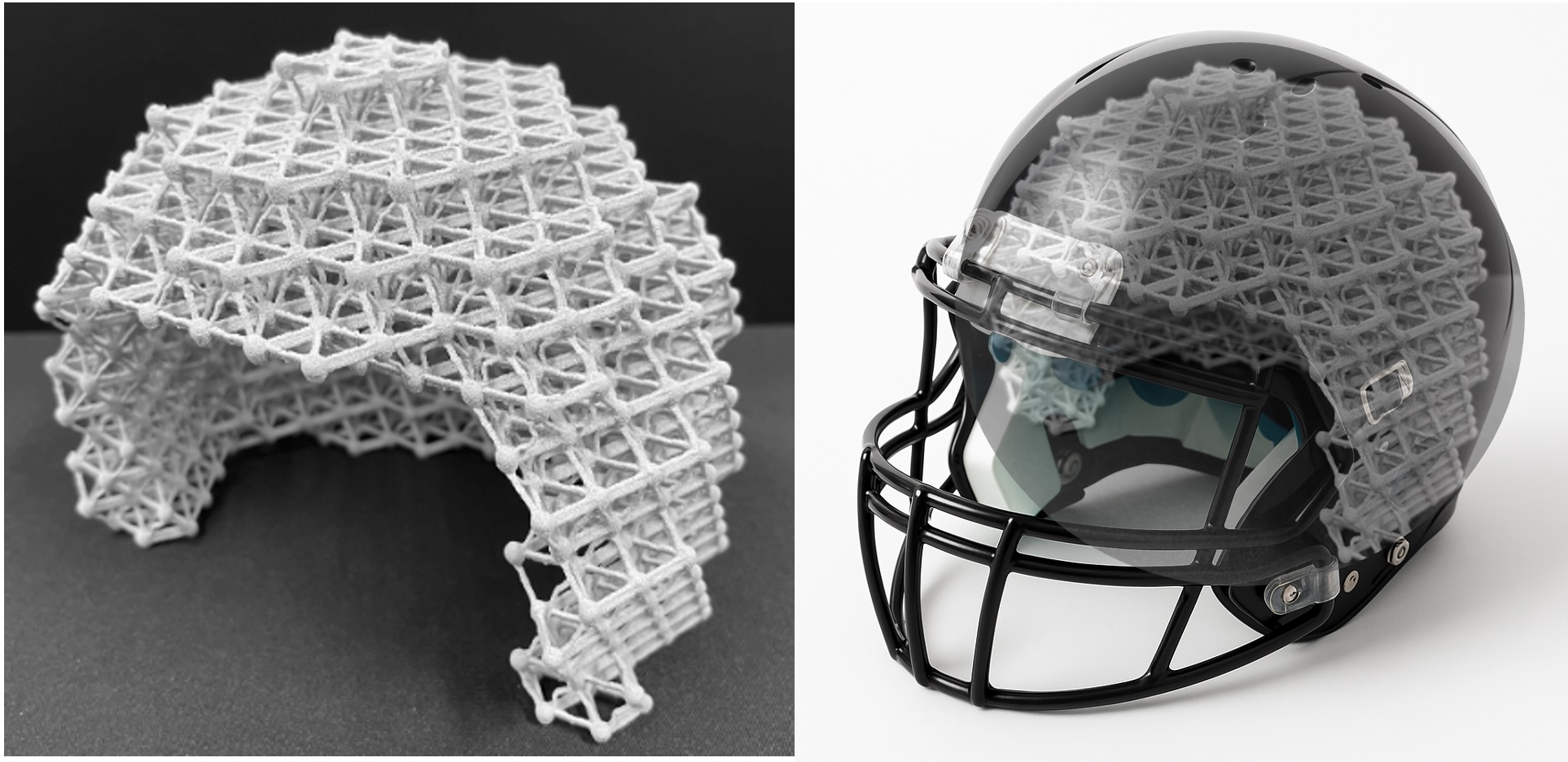
Additive Manufacturing (AM) は、任意の形状を持つ格子構造を製造することを可能にし、基材では本来発現しない特性を実現することを可能にします。これにより、希少元素への依存を軽減し、代替元素を活用することが可能になります。この目的を達成するためには、AMで製造可能な形状において、結晶構造や電子構造に由来する物質特性を再現するモデリング技術の開発が重要です。この概念を「Atom-Mimetics(アトム・ミメティクス)」と呼び、私たちの機械的メタマテリアル研究の基盤としています。 構造と特性の関係を理解し、その理解に基づいて構造を制御する能力は、材料開発における鍵となります。基礎的な取り組みとして、電子構造に関連する材料分布を操作することで弾性特性を制御しようとしています。しかし、研究を進める中で、これが実際には非常に難しい課題であることが明らかになりました。 この課題に対応するため、熱応答性を持つバイメタルビームを応力誘起型の相変態格子に組み込むことで、時間依存的な形状記憶効果を示す4Dメタマテリアルを開発しました。これらの材料は、特定の元素組成に通常関連付けられる特性を模倣する可能性を示しています。特に、相変態を活用してエネルギーを吸収する機械的メタマテリアルは、衝撃吸収材や免震材として注目されています。既存の相変態型セルラー材料(PXCM)は主に体積変化を伴う相変態に依存していますが、これは実際の材料ではほとんど見られません。金属材料におけるマルテンサイト変態に着想を得て、平行四辺形型の双安定メカニズムに基づくマルテンサイト型PXCM(MPXCM)を提案しました。これにより、体積変化ではなく剪断変形を通じた相変態が可能となり、より安定したエネルギー吸収が実現します。この設計手法は「Atom-Mimetics」の概念により合致しています。 結晶材料における弾性率やその異方性を再現する格子の設計は、弾性率の異方性およびその変化を相変態の前駆現象として模倣するメタマテリアルの設計において重要です。本発表では、結晶構造を模倣した格子の弾性異方性、および応力誘起型・熱誘起型の相変態を示す格子の構造-特性関係についての研究を紹介します。これらの知見は、AMを活用したメタマテリアル設計のさらなる発展への道を開くものです。
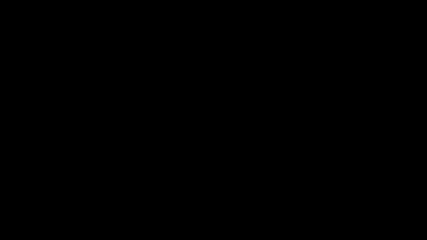
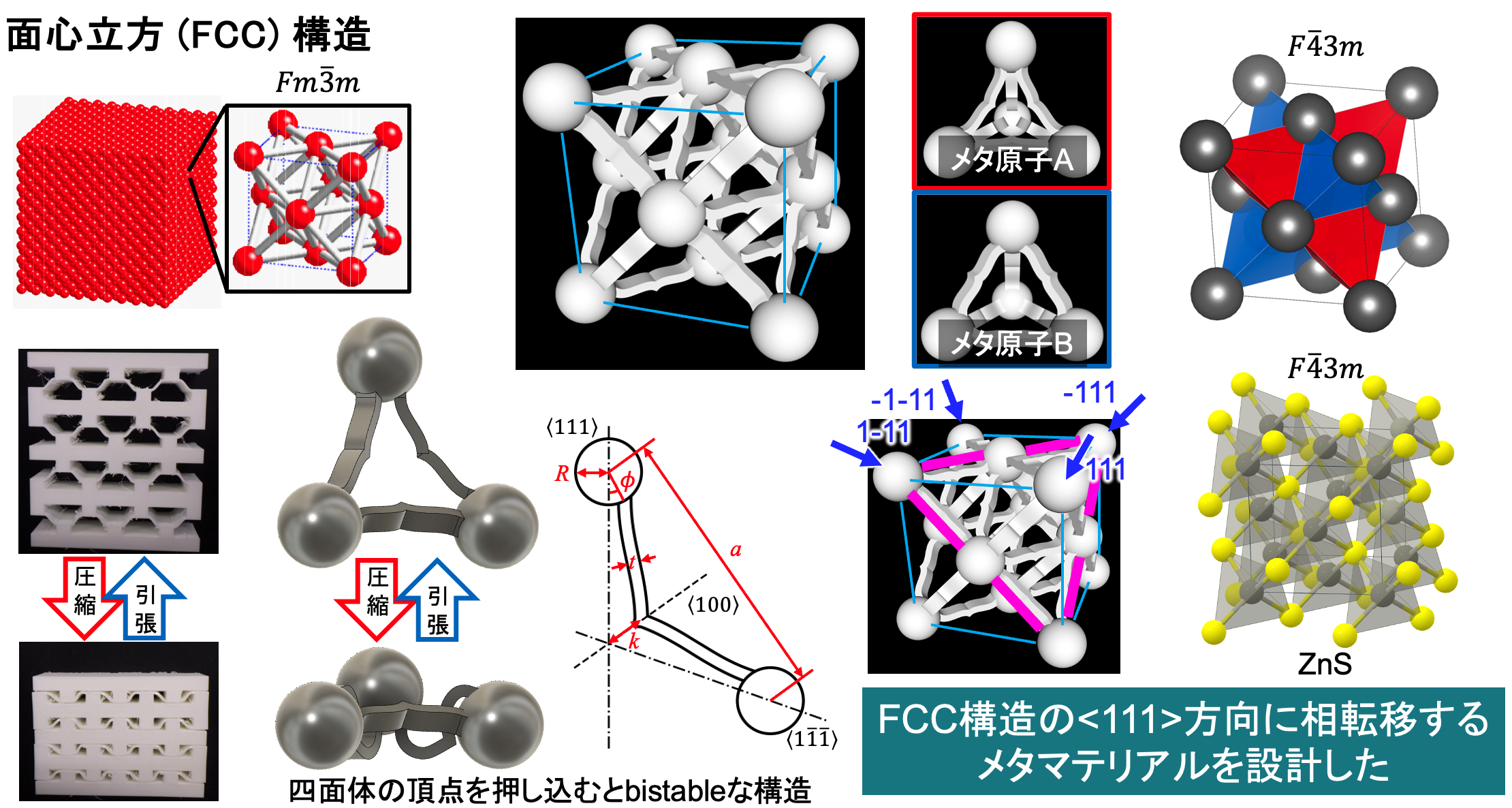
材料の構造と特性の関係の理解とそれに基づく構造の制御は新材料創成の基礎となっています。 一方、付加製造(AM)技術の発達により、サブミリメートルからメートルレベルの構造制御が可能となりました。AM技術と、これまでの物質・材料科学で得られてきた原子レベルの構造と特性の関係の知見を融合した格子構造の設計により、その物質が本来有さない特性を発現させることが、新しいメタマテリアル創成手法として期待されます。本研究では、その基礎として、電子構造と弾性特性の関係を元に、材料の密度分布制御で弾性特性や相転移の制御を試みます。これにより、希少元素組成でしか発現し得なかった機能性を、他の元素で発現させるための指針を示します。これを、AMで付与した形状が力学や温度場で構造変化するメタマテリアル設計に活用することで、持続可能な発展に資する新技術の学術的基盤構築の基礎とすることに挑戦します。本研究は、大阪大学基礎工学研究科尾方成信先生、早稲田大学基幹理工学部 竹澤晃弘先生との共同研究です。(2025年度科学研究費挑戦的研究(萌芽)「原子間結合の模倣による力学的メタマテリアルの設計手法の探索:4Dプリントへの応用」)